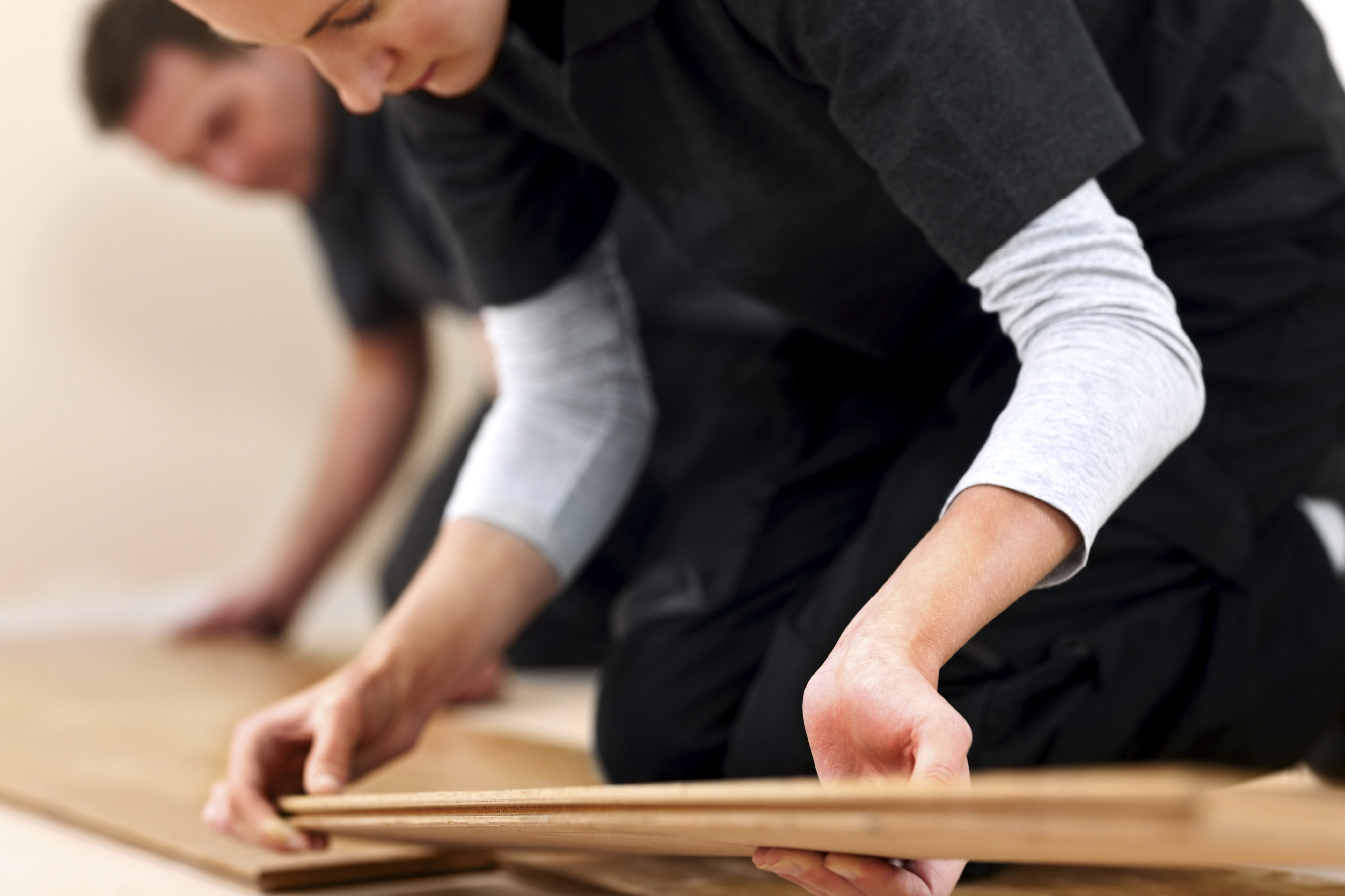
The appeal of wood is its natural makeup and warm texture. But that which most attracts us to hardwood flooring is also the reason for most of the call backs flooring installers have to deal with. When problems occur, inspectors must determine who the culprit is and it’s usually moisture. Understanding how moisture affects a flooring and sub-flooring installation can help you to avoid problems and expensive call backs.
Wood and Moisture
Wood is made up of small cells which are hydroscopic; porous and capable of absorbing moisture. When flooring is exposed to moisture from ground water, leaks or plumbing, it will absorb this water and expand.
Wood also absorbs ambient moisture and will expand during warm, humid months and contract during cold or dryer times. If the expansion and contraction of the wood happens too quickly or if there is no space for this movement to take place, flooring problems will occur.
Here are some of the most common hardwood flooring problems and how to overcome them:
Cupping
A moisture imbalance in the wood causes the boards to curve with the edges being higher than the center. This can be caused by ambient moisture or moisture under the flooring which cause the boards to expand. If insufficient room was left between boards for expansion, cupping occurs as the edges of the expanding boards are forced upwards.
Crowning Floors
Crowning occurs when the center of the floor is higher than the edges. This is caused when flooring absorbs ambient moisture and expands beyond the space provided during installation. With no place to go, the expanding boards push up in the middle. Crowning is common on cupped flooring which has been sanded before it has properly acclimated to the ambient atmosphere in the home. New boards tend to have more moisture and this may result in cupping, but when those boards dry, the sanded edges shrink even further, leaving the center raised.
Buckling
An extreme form of cupping, buckling usually only occurs after flooding or when the moisture difference between subfloor and flooring is too great at the time of installation. The flooring expands to such an extent that the boards pull away from the sub-flooring. This usually requires reinstallation.
Gaps
If the flooring is not properly acclimated prior to installation, it can lose a lot of moisture which results in gaps between the floorboards. The wider the board, the wider the gap is likely to be. Gaps can be caused by ‘hot spots’ where heating or cooling ducts cause some areas of the flooring to experience different ambient moisture conditions.
Squeaky floors
If insufficient room has been left between sub-flooring panels or floorboards, the constant expansion and contraction of flooring may serve to loosen nails. As you step on the floor, the boards move down the nail shaft or rub against other parts of the flooring system resulting in squeaks.
Preventing Flooring Problems
Measure the moisture content of the flooring and the sub-flooring to mitigate problems and to ensure that flooring components are properly acclimated prior to installation. There are tolerances for moisture content that need to be met before installation begins. Those tolerances vary depending on the flooring species, board width etc.
Installing any flooring means you have accepted the floor and all conditions are met. Always consult the manufacturer’s instructions to ascertain the ideal moisture content for your flooring system, for storage instructions onsite and for instructions on how to install your floor to allow enough room for expansion and contraction. Don’t assume the instructions are the same as the last time.
Remember it’s cheaper & easier to avoid problems than to fix them later.
Always follow your manufacturer’s instructions on proper sub-floor panel spacing.
Use a wood moisture meter to measure the moisture content of your flooring components before, during and after installation.
Get a copy of the National Wood Flooring Association installation guidelines and methods here.